Cubic printing technology. A magic trick available for designers and companies
Cubic printing technology. The first time I heard about this decorative process, I was impressed and curious about its name.
I thought, what is this all about?
Some kind of pictorial or artistic process invented by Picasso during his Cubist period?
(Reading time: 11min 35s)
For sure none of this, but there is something artistic in one of the most fascinating and magic industrial processes I came across in my activity as designer.
Even if it’s a long- established technology with many applications, it’s still unexpectedly not well known, as I could personally notice each time that I suggest its use.
In the last days I have been contacted by CUBIK SERVICE srl based in Pasiano di Pordenone, Italian leader company for the Cubic Printing® process founded back in 1987.
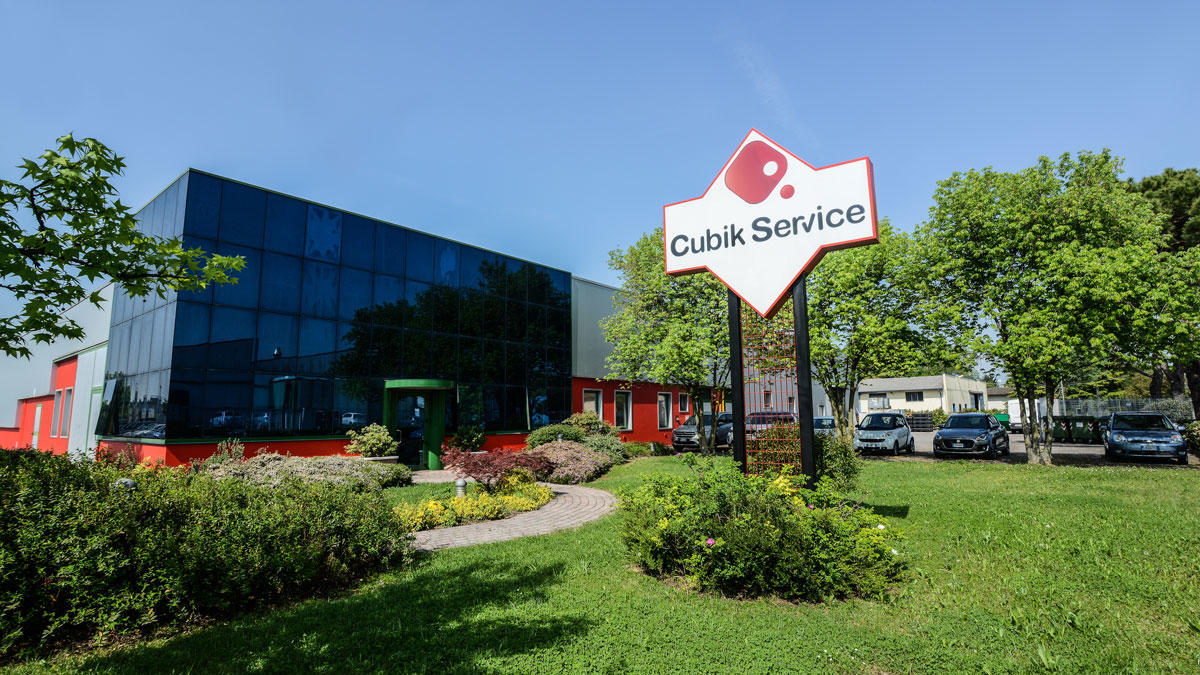
The technical and informative material they sent me was very interesting, so that it additionally aroused my curiosity and wish to clarify some details that were not clear to me.
Visiting a company, speaking with the Management and watching personally how some processes work is, from my point of view, the best way to know and understand technologies and industrial processes.
So I decided to contact them and organize a meeting at their production plant.
The answer came immediately in a few days and I was welcomed at the company by the smiling and kind face of Silvia LANFRIT, in charge of the Marketing and Business Development by CUBIK SERVICE, I asked her the first main question:
Silvia, what is the cubic printing process?
“The cubic printing method, called also hydrographics or watertransfer printing is a process by which it is possible to apply decorations on three-dimensional objects.
Through this process that you will see then in our production plant, it’ s possible to transfer a drawing or a texture on all (or almost) three-dimensional objects.”
What's the meaning of its name?
“ The cube is the three-dimensional geometrical figure par excellence, therefore the name “cubic” highlights the capacity of this technology to adapt a two-dimensional décor to a three-dimensional object.
How and when was this technology born?
“ Three Japanese companies contended the authorship of the invention and TAICA CORPORATION claims to have invented it in 1974, by the way the first Patent was registered by the company KABUSHIKI KAISHA CUBIC ENGINEERING on 26th July 1982.
As often happens, also this invention was born by chance.
It is reported that the company charged one of its engineers to decorate an hair dryer, this was not an easy issue since at that time the technology allowed to decorate only flat surfaces, not complex or three-dimensional shapes.
He made a lot of trials but without success until one day he “luckily” got sick.
At the time, it was common for the Japanese to take powdered medicine by wrapping it in thin starch sheets, called oburāto, which made it easier to swallow.
When the engineer was preparing his medicine, he accidentally dropped an oburāto into a cup of water.
Reaching into the glass to fish it out, he found that the wet oburāto wrapped around his finger, matching its shape perfectly.
From that small accident the solution to the problem was born!”
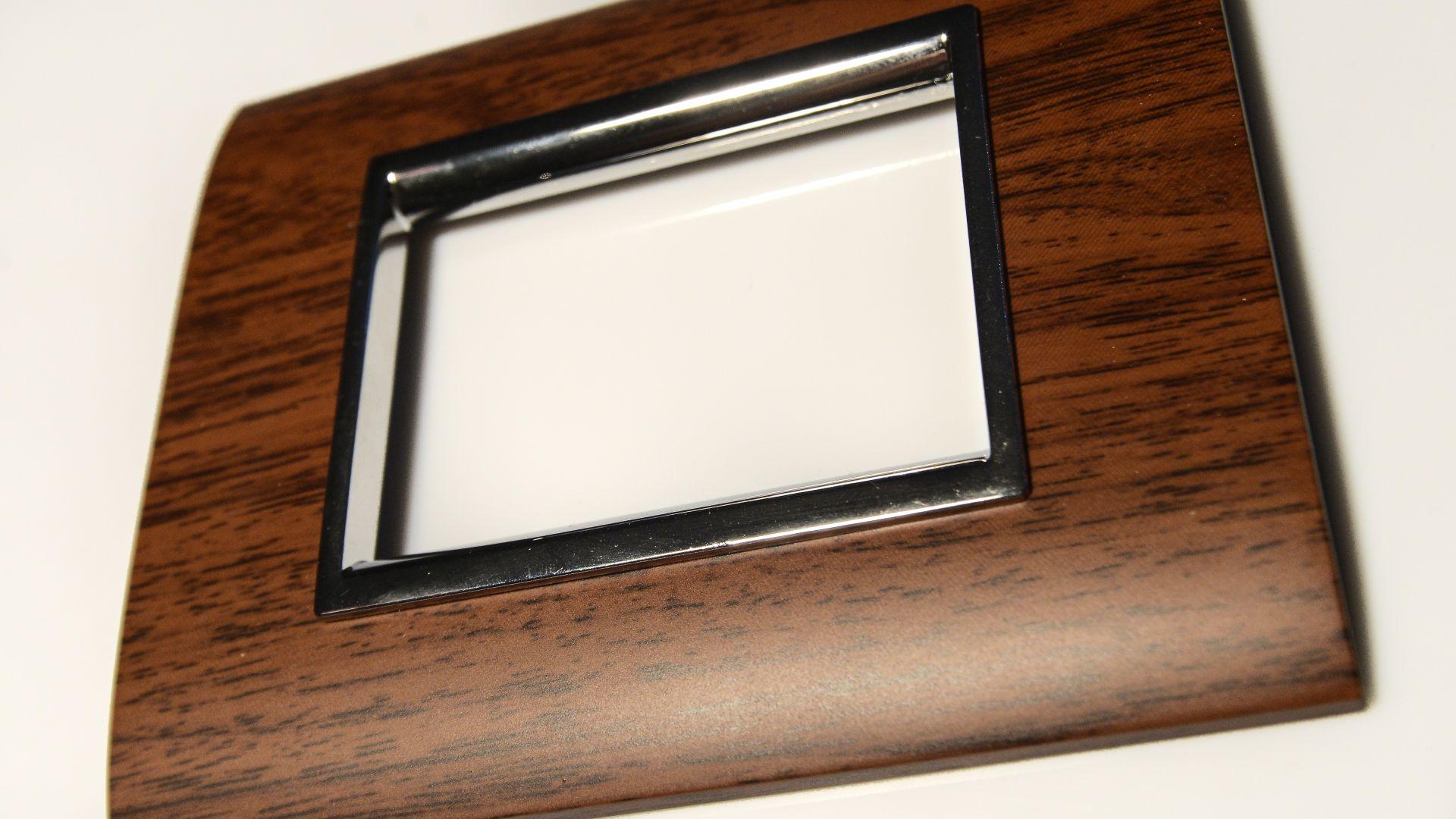
On what materials is it possible to apply this process?
“Basically on all solid materials, such as: metal, glass, ceramic, plastic, fiberglass, wood and different alloys.
At last all materials that could be painted and dipped in the water, that as we will see later, has a key role in the cubic printing process.”
What are the shapes and objects that could be decorated?
“All materials with the features we already mentioned.
There could be different shapes, this enables us to work in different fields such as automotive, biomedical, household, sport devices and furnishing to give you some examples.”
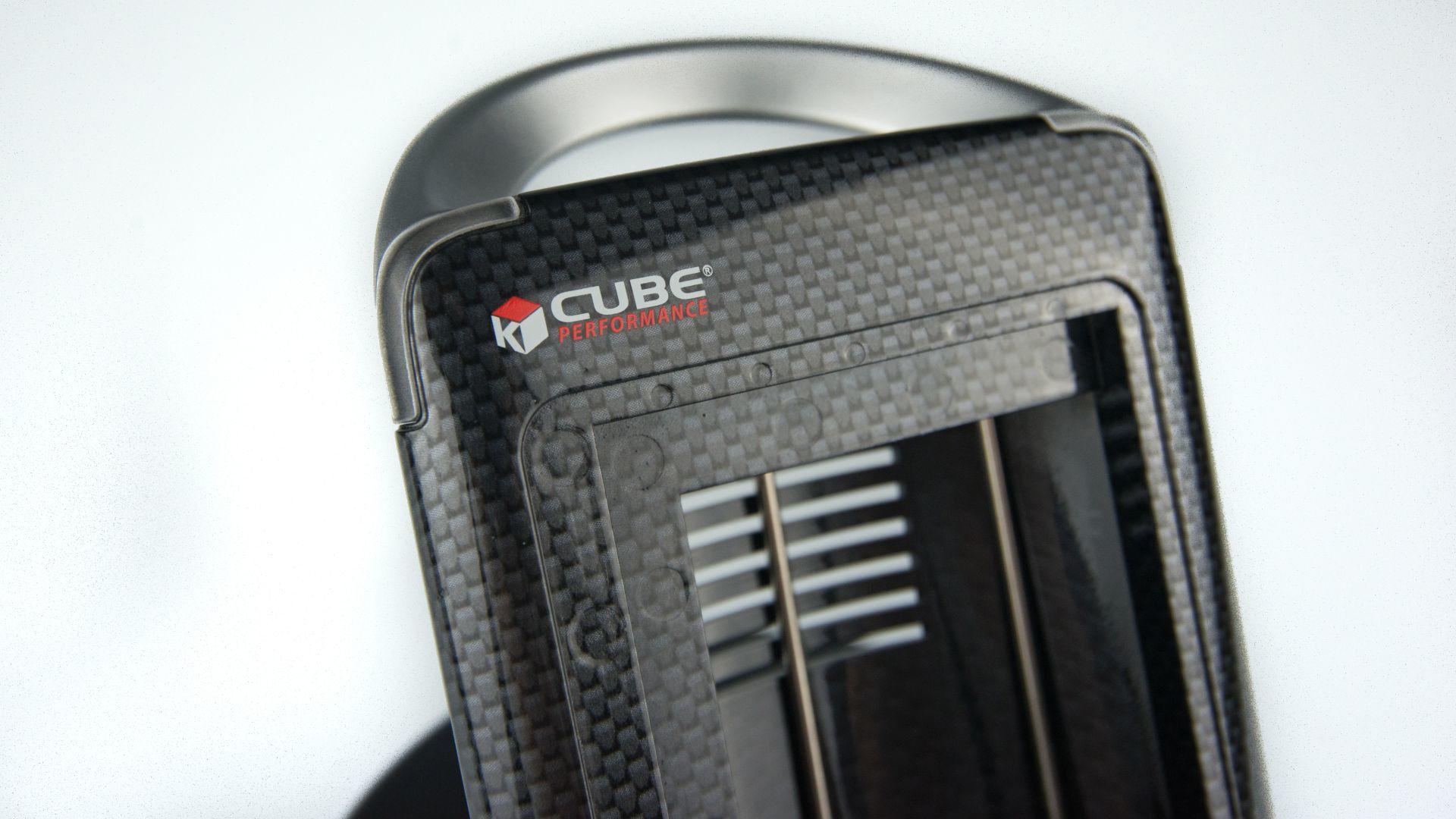
How are the decorative films made and what are their features?
“It’s a transparent foil made of PVA (Polyvinyl Alcohol) with a few micron thickness, soluble in water, on which the graphic image that should be transferred, is printed in high definition.
The decorative films have been renewed during the last years both for the quality of the image and the range of drawings available.
In this respect CUBIK SERVICE is, among the Italian licensee, the first company to propose in Europe the new technology S-CUBIK, now present only in the U.S.A., China and Japan, that could confer to decorations and finished parts a quality and sharpness of the images never experienced before.”
How many and what kind of decorations are available?
“The available decorations on the market are countless.
There are some films that reproduce the appearance and finishes of real materials, such as wood, metal, carbon, just to mention some of them, and an infinite number of three-dimensional textures with geometrical and artistic drawings.
Our company put at our customer’s disposal a catalogue of finishes and decors that could satisfy every need but we could offer also personalized decorations with exclusive use.”
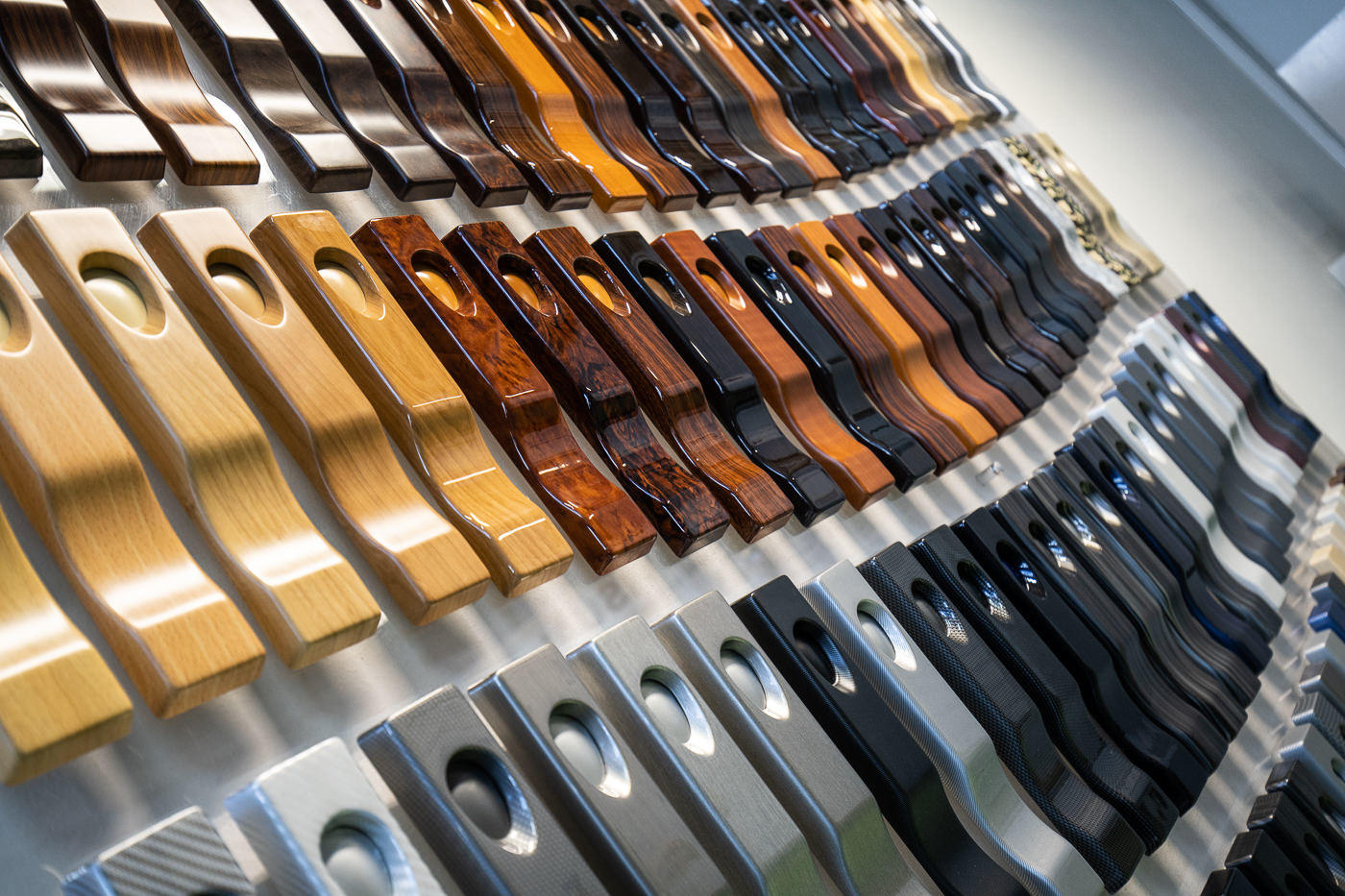
How does it works and what are the phases of the cubic printing process?
“The main element for the decoration of a product through this process is the same that allowed the process of perfect adhesion of the starch foil to the finger of our Japanese friend: the hydrostatic pressure of water.
In order to make the magic happen, additional steps and processes are necessary, these could be described mainly as follows:
Phase 1 – Preparation of the part
It’s the first phase and it’s very important because if not executed in the right way, it could compromise or even avoid the success of the operation.
The part to be decorated is perfectly cleaned and, if necessary, polished and varnished with a color that is suitable for the kind of decoration and finish requested. The varnishing has also the purpose to enhance the attachment of the ink to different surfaces.
Phase 2 – Preparation of the film
The activator, a chemical compound, is sprayed on the decorative film to permit the dissolution of the foil when dipped in the water.
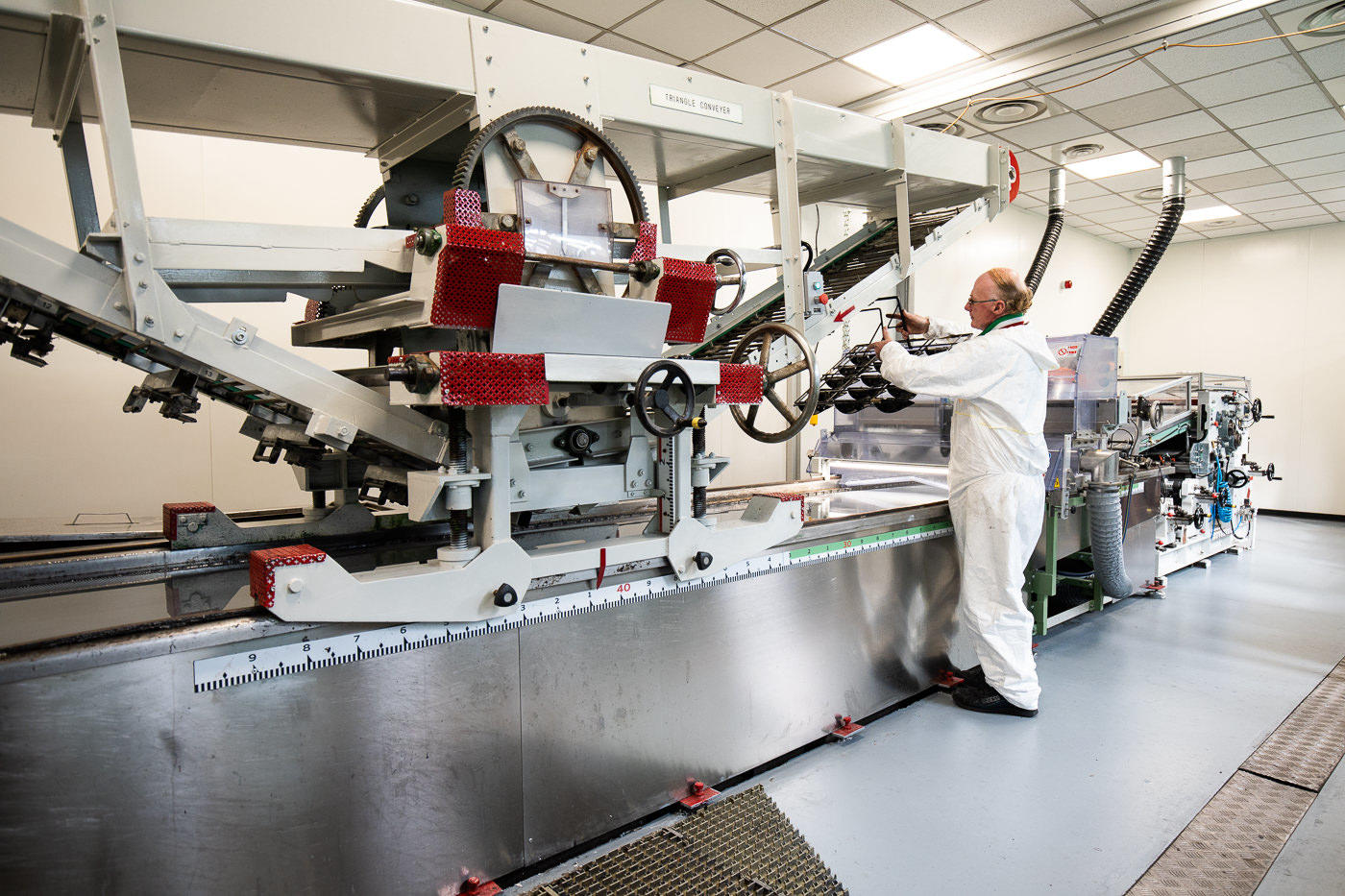
Phase 3 – Positioning of the film in the water tank
The film is positioned on the surface of the water that is contained inside a tank made of steel and equipped with a control panel that allows the automatic managing of the process.
Phase 4 – Dipping of the part
After that the decorative film is activated, the dipping phase could start.
This is an operation that should be realized gradually and with a speed that could be managed to control the decorative effect on the part.
During the dipping, the activator, applied earlier on the film, dissolves the texture on the foil whereas the hydrostatic pressure of the water impresses the drawing on the part (see following image).
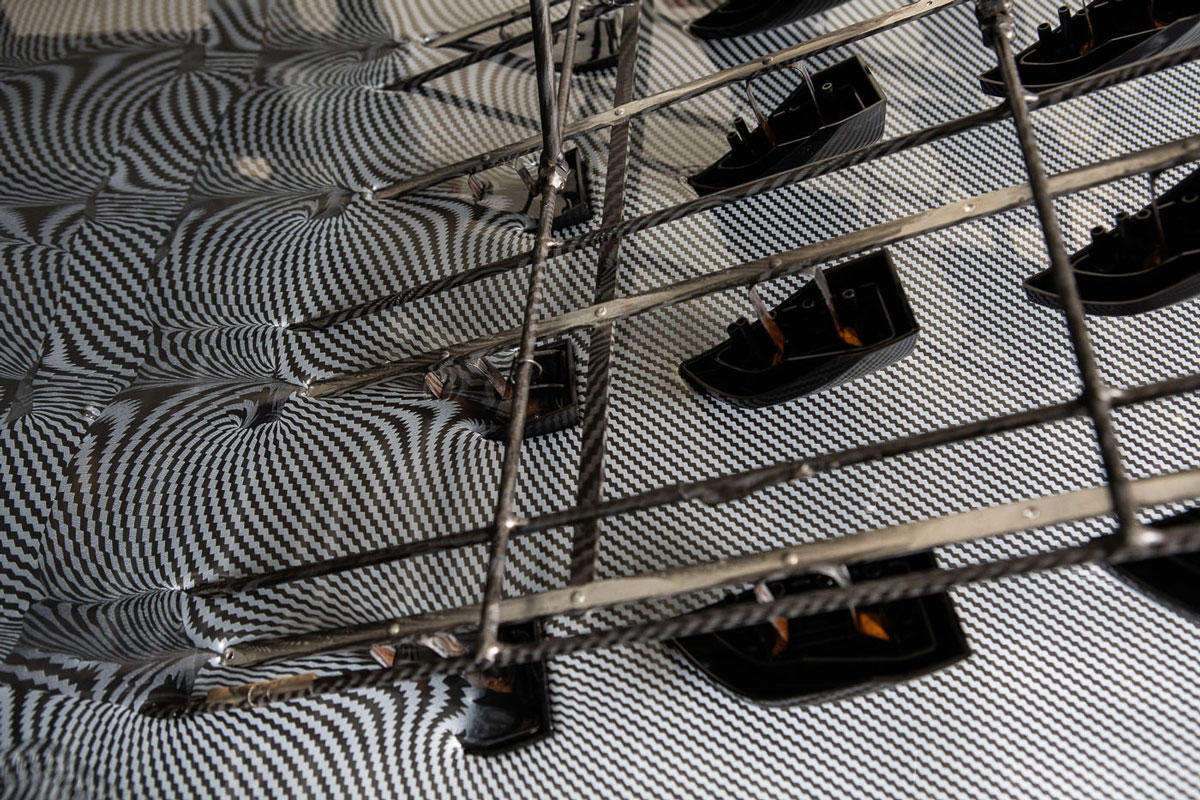
Phase 5 – Rinsing and drying
Once removed from the tank, the part is rinsed through high pressure water sprays that remove the remaining jelly wastes of film and, at the end, passes through industrial ovens that dry it perfectly.
Phase 6 – Application of the protective paint
The last phase of the entire process foresees the spray application inside appropriate automatic painting cabins of a protective transparent coating that could be glatt or matt based on the aesthetical result needed.”
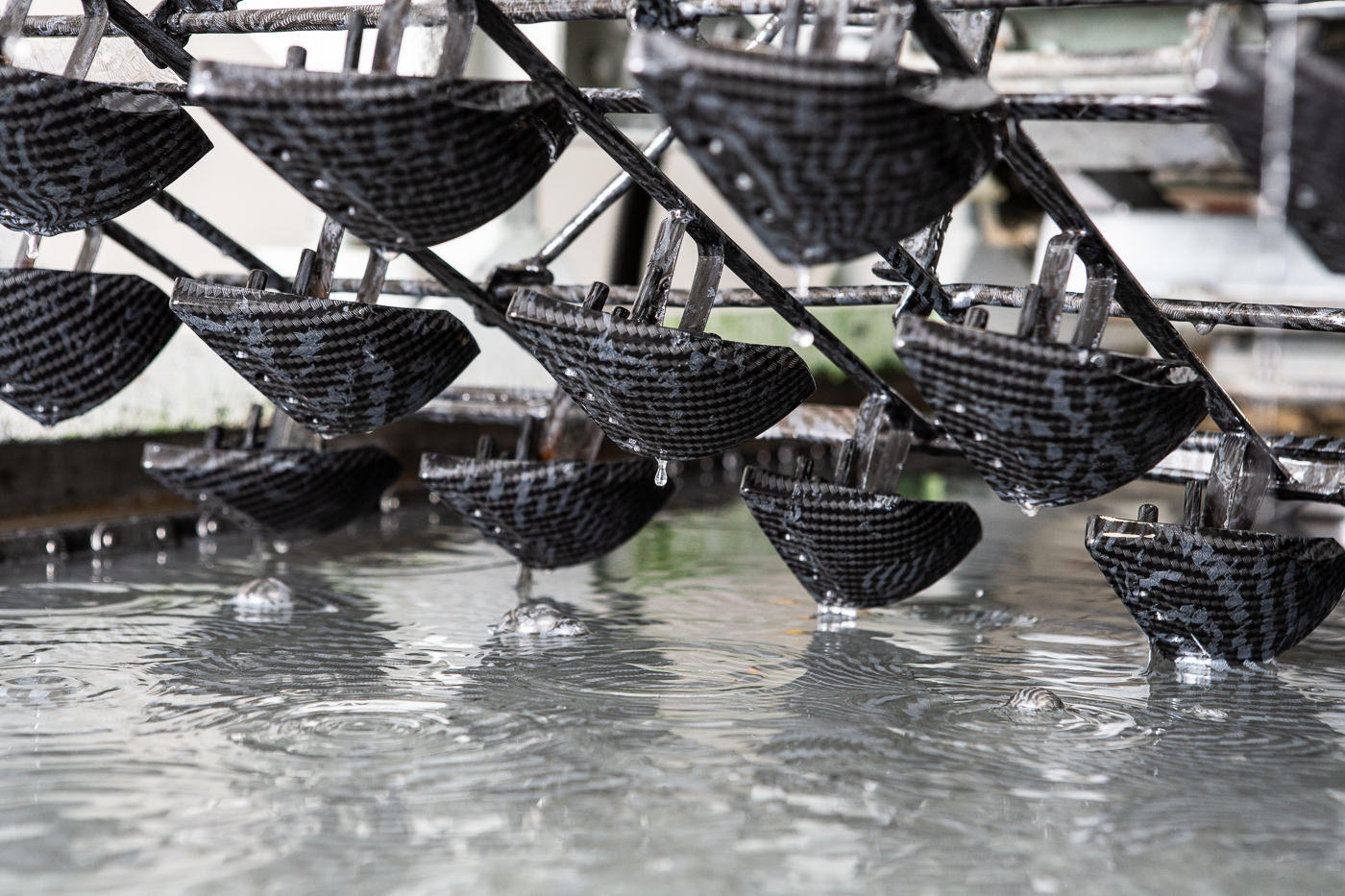
Why is cubic printing advantageous?
“There are many advantages in this technology.
As we said, it allows the decoration of complex small and big shapes, moreover it’s possible to create aesthetical variations of already existing products without modifying the molding equipment, that means with a minimum investment.
Compared with other decorative technologies IMD (In Mold Decoration) and IML (In Mold Label) the cubic printing process is more versatile and cheaper because permits the decoration of every existing component in comparison with other technologies that need to create specific molding equipment and expensive automation facilities.
It’s also possible to prepare samples with different effects in a simple, cheap and quick way (just by changing the decorative film) giving customers the possibility to evaluate a prototype that will be identical to the final part in series production.
Also the cost of the film compared to IMD and IML is much lower and it’s possible to develop decorative films personalized on customer’s request.
CUBIK SERVICE thanks to its direct partnership with the Japanese supplier of the films, could realize it in a very short time.
What are the limits?
“Technically there are some limitations.
We could decorate very complex shapes but we couldn’t guarantee the same alignment of the decorative pattern on all parts, that therefore turn out to be one-of-a-kind products with minimum differences.
Another limitation is the size of the parts that could be processed that depends on the dimension of the tank, CUBIK SERVICE could handle parts with maximum length of 2 meters and 60cm width.
From an economic point of view it’s more expensive than a standard painting because, as you could see, the process involves additional phases.
This is however partially true since some kind of paints have reached very high costs on the market.
By the way it’s possible to reduce the costs of the cubic printing process by applying the film directly on the raw part, if the material and base color allow it, so that the process is reduced to two phases: cubic printing and topcoat (protective paint).
Finally, the cubic printing process, compared to IMD decoration (In Mold Decoration) is economically competitive on medium production range, that is about 60/70 thousand parts/year.”
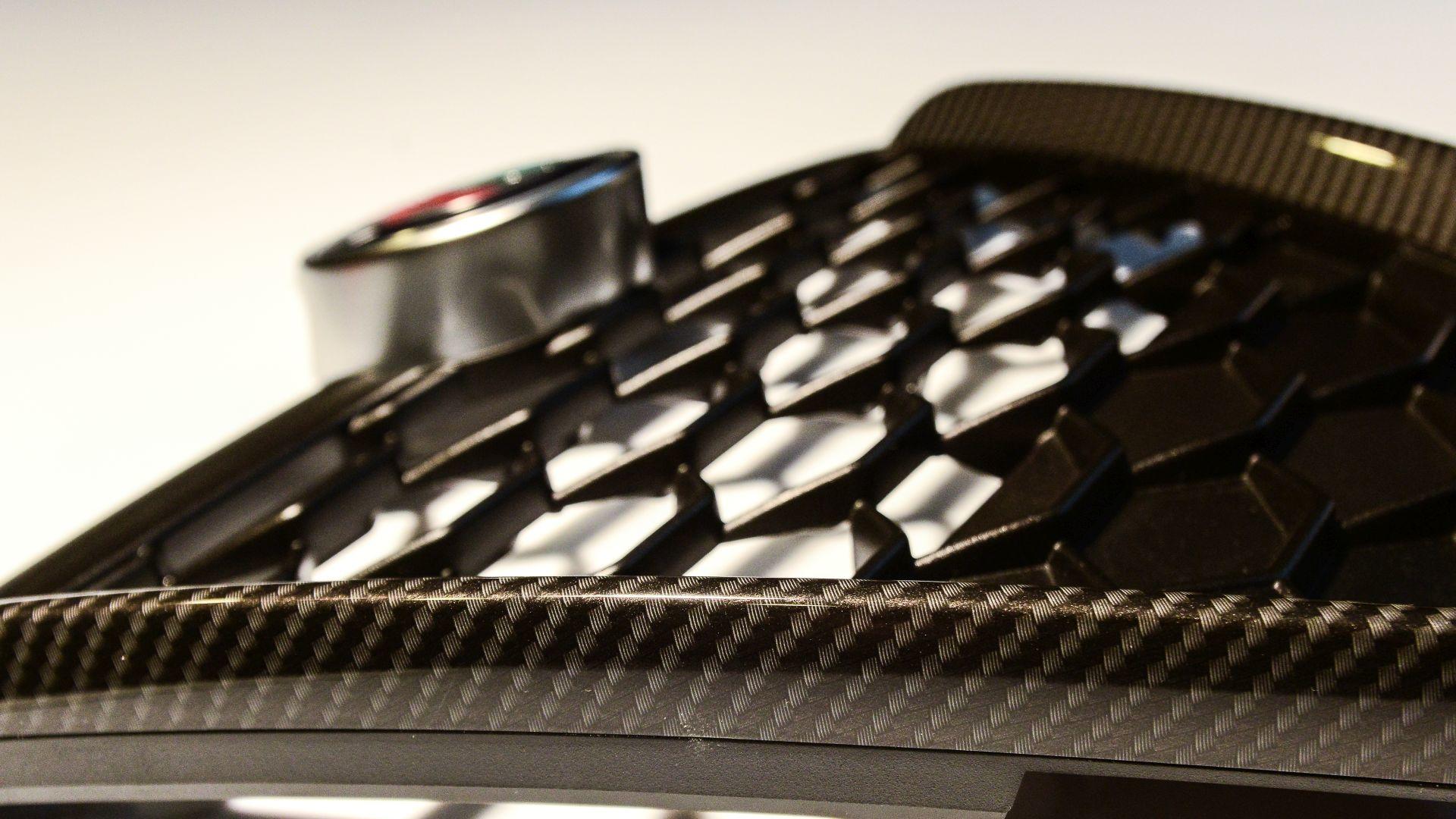
Are the decorations applied durable?
“If you are not well informed about the cubic printing process, it’s easy to get the wrong idea and think that a decoration applied using a thin foil dipped in the water could not guarantee a sufficient wear resistance.
This is not true, since the décor is protected by more layers of painting that confer it an excellent protection against scratches, atmospheric agents and UV rays. The decoration this way is durable over time, doesn’t yellow and doesn’t peel off.
One of the main sectors of CUBIK SERVICE is the Automotive, where we realize a lot of internal and external car components, that means parts that undergo high levels of stress and wear, such as bumpers, rear-view mirrors, rims, etc.”
Is cubic printing process ecofriendly?
“Yes, definitively.
As I told you it’s a very clean ad natural element, as water, that allows this process, this is not wasted but re-used many times before it’s changed and recycled thanks to an automatic self-cleaning system that at the end of each process filters and removes all film and activator’s wastes.
The industrial cubic printing process is automated (see following picture), handled by software that precisely settle each phase timing consuming only the necessary energy and eliminating energy waste caused by human mistakes.
The paints that are used are water-based according to current regulations and the painting processes, also robotized, are executed inside cabins equipped with aspiration hoods and grates to collect dust, so that they could be disposed safely and ecologically.”
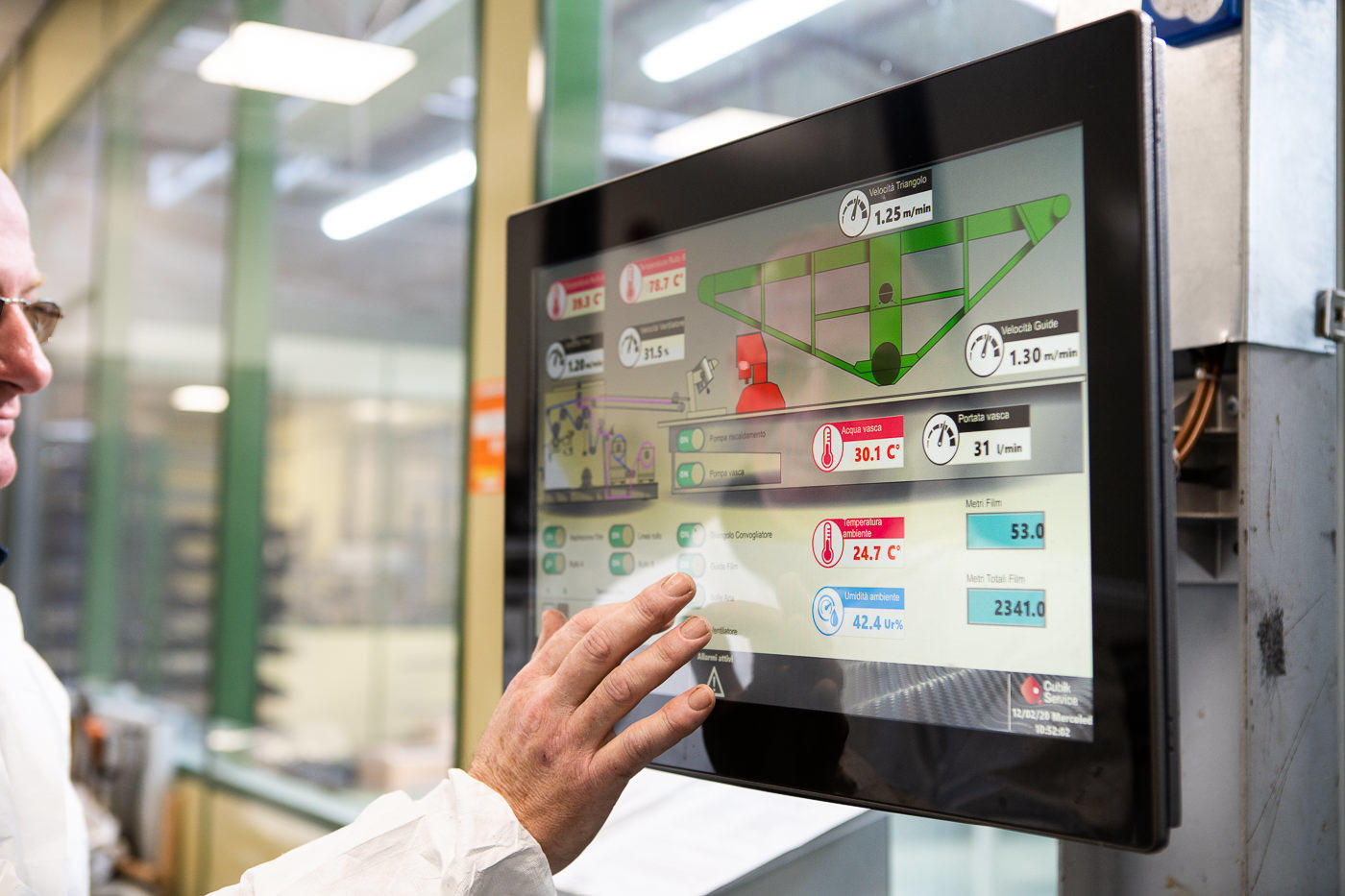
Could products decorated with cubic process be disposed and recycled?
“At the end of this process all that remains on the surface of the object is only the ink of the decoration since the film, once dipped into water, dissolves completely.
One object decorated with cubic printing and one painted are disposed exactly in the same way, since the thickness and consistency of the ink are negligible at all.”
In conclusion: what are the updates in this sector?
“Technologies and materials are in continuous development in every area and sector. Also the cubic printing process is following this trend.
During the last few years some progress has been made as regards both equipment and materials, bringing the variety and quality of the decorations to a level never expected before.
I told you about the new technology S-CUBIK that we now put at our customer’s disposal and soon there will be the possibility to have a touch effect on the parts.
Moreover we are developing the BACKLIGHTING CUBIK a special technology that combines the cubic printing process to the laser cut. It’s therefore possible to engrave the rear of the part creating drawings, letters and numbers that are visible on the front part only once enlightened (see image here below).
This solution is suitable for many uses, when it’s necessary to add light indicators without compromising the clean and linear design of the product.
A technology that could support and help a designer, don’t you think so?
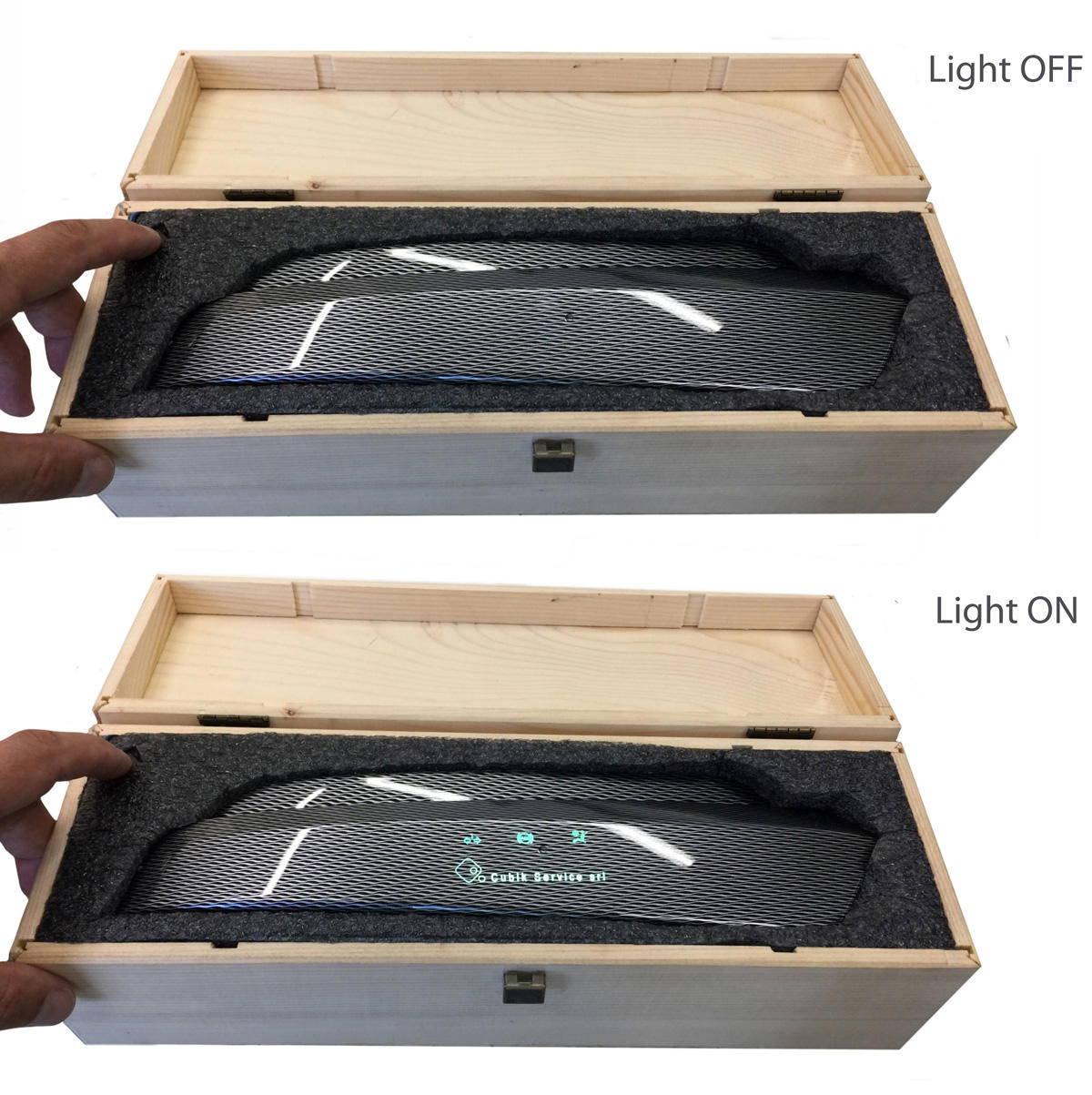
It was interesting and informative to spend some time with Silvia, since I came out from CUBIK SERVICE with more clear ideas and many interesting inspirations for my future projects.
The cubic printing process is a fascinating process, not only for how it’s made but also for its unique capacity to give nobility and aesthetical quality to “poor” materials such as plastic.
I thank again CUBIK SERVICE for its availability and especially Silvia LANFRIT, for the support and…the coffee! (;-D
For those who want to have more information about this issue or ask information: www.cubikservice.com
Write me or contact me to share experiences and information or to suggest me more topics I could describe in my next articles.
See you soon.